Technical Blog
Developing a Robust PSM Program: A Practical Roadmap
Implementing a comprehensive Process Safety Management (PSM) program can be a complex task—especially for organizations starting from scratch. Whether driven by regulatory requirements or a proactive safety culture, building a program that is both effective and sustainable takes planning, collaboration, and technical discipline.
In this blog, we share a generalized approach based on lessons learned from supporting facilities across various industries in developing their PSM systems. The insights below offer a practical roadmap for companies looking to elevate their process safety practices.
Common Challenges in the Absence of a Formal PSM Program
Organizations without a mature PSM program often face issues such as:
- Lack of a structured safety management framework
- Incomplete or outdated process safety information
- Minimal hazard awareness among personnel
- Informal or inconsistent Management of Change (MOC) processes
- Gaps in emergency preparedness and equipment reliability programs
- Misapplication or non-application of required Recognized and Generally Accepted Good Engineering Practices (RAGAGEP)
- Failure to apply PSM requirements to all covered equipment
These challenges not only increase operational risks but may also lead to non-compliance with OSHA 29 CFR 1910.119 or similar process safety regulations.
A Phased Approach to PSM Implementation
A phased, scalable approach to building a PSM program can ensure manageable progress and lasting success. Here’s a typical progression:
-
Applicability & Scope
Determination of limits of the covered scope of the process.
Determination of applicable RAGAGEP.
-
Process Safety Information (PSI)
Gather and validate data on chemicals, process technology, and equipment design.
Update P&IDs and H&MB to reflect actual operations.
Develop Safe Operating Limits of process equipment.
Revise facility siting information (e.g. plot plan, Electrical Area Classification, safety diagrams).
Confirm design and documentation of safety systems (Relief / Shut Down Systems (SDS) / Fire Protection).
-
Process Hazard Analysis (PHA)
Conduct a structured hazard analysis (e.g., HAZOP) with a cross-functional team.
Prioritize recommendations and establish a tracking system for resolution.
-
Operating Procedures
Develop standard operating procedures for startup, shutdown, normal, and emergency operations.
Develop and revise safe work practices (Hot Work, LOTO, permitting process).
Ensure alignment with actual field practices.
-
Training & Workforce Engagement
Roll out general PSM awareness training to all employees.
Provide job-specific training for operators and maintenance personnel.
Encourage safety ownership through communication and feedback channels.
-
Mechanical Integrity (MI)
Identify covered equipment and specify applicable RAGAGEP. This usually includes categorization of safety critical items.
Consolidate design documentation for equipment and develop Inspection, Testing, and Preventative Maintenance (ITPM) plan.
Develop procedures for addressing maintenance, repairs, deficiencies, personnel requirements, and quality assurance.
Implement a documentation system to track asset condition, required activity, deficiency management, and maintenance history.
-
Management of Change (MOC)
Formalize an MOC process with defined roles, technical review steps, and pre-startup safety checks.
Ensure changes are communicated and documented properly.
-
Incident Investigation & Emergency Planning
Develop standardized procedures for incident investigation, root cause analysis, and communication to workforce.
Develop Emergency Response Plan and coordinate drills and planning with internal teams and external responders.
-
Compliance Audits & Continuous Improvement
Schedule periodic internal audits to assess effectiveness and identify gaps.
Use findings to improve procedures, training, and overall program maturity.
Tangible Benefits of a Strong PSM Program
Organizations that invest in a well-executed PSM program can yield meaningful results, such as:
- Improved safety culture and awareness across the organization
- Enhanced regulatory compliance and audit preparedness
- Proactive risk management through better hazard identification
- Significant reduction in frequency and severity of highly hazardous chemicals
- Increased equipment availability, improvement of quality, and ability to manage lifecycle of equipment through disciplined maintenance
- Stronger emergency readiness and response capabilities
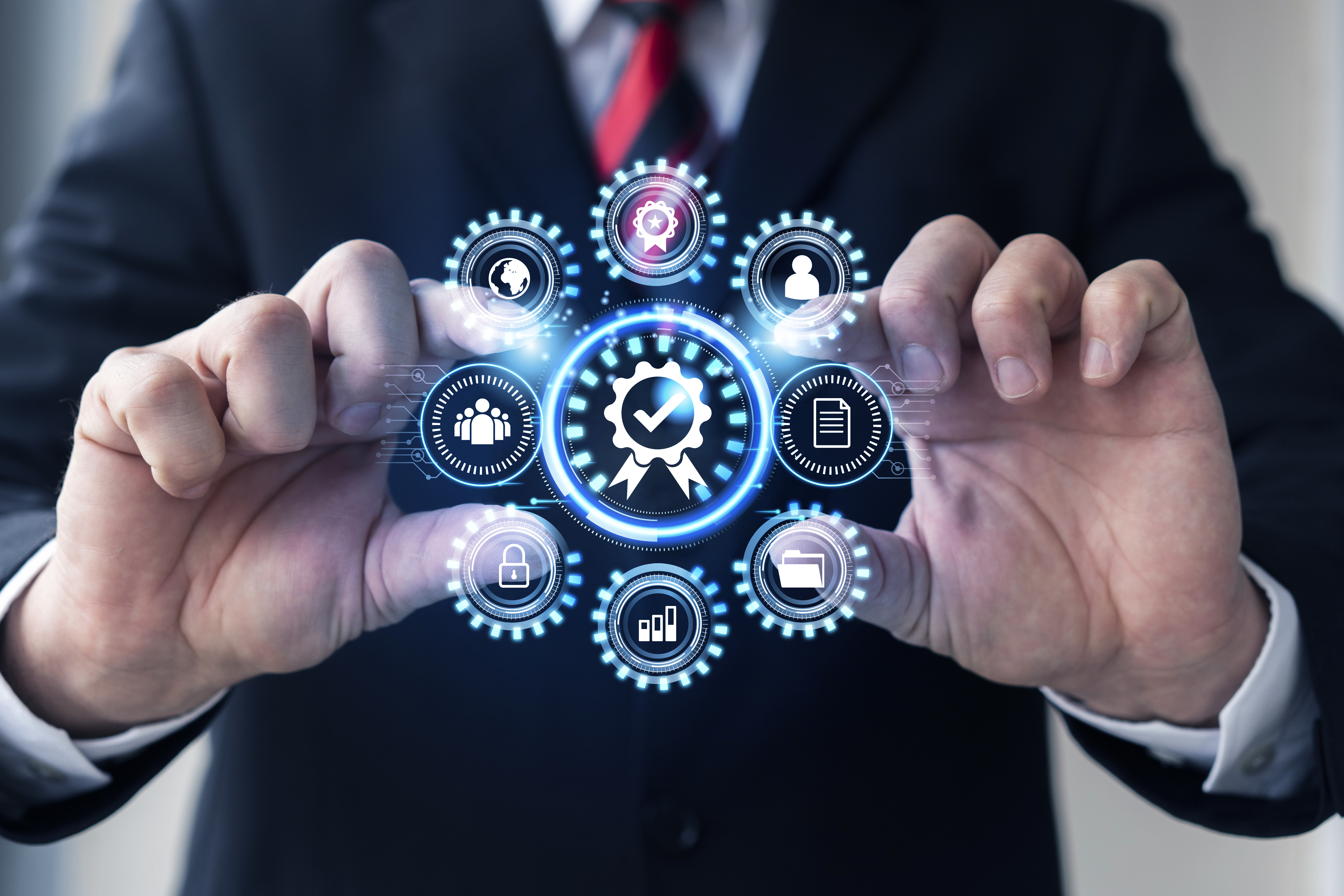
Final Thoughts
Developing and implementing a PSM program requires commitment, collaboration, and consistency. Whether your organization is starting from scratch or revamping an outdated system, a phased, practical approach—grounded in regulatory requirements and operational realities—can drive measurable improvements in safety and performance
Looking to implement or strengthen your PSM framework? Our team brings deep technical expertise and field-proven methodologies to help you succeed.
Meet the Author
Billy Wimberly, CSP – PHA Facilitator
Billy is an experienced chemical engineer with 15+ years of industry experience. He has specialized in the evaluation of process safety programs. He has facilitated numerous What-If, Inherently Safer Design (ISD), Hazard Identification (HAZID), Hazard and Operability (HAZOP), Safety Over-ride Risk Assessments (SORAs), Fault Tree Analysis (FTA), and Layer of Protection Analysis (LOPA) risk assessments.
Related Cognascents Solutions
At Cognascents, we have the expertise to meet your needs. Explore the variety of related services we offer and discover how our tailored approach can support your business.
Our mission is to empower our clients with innovative solutions that enhance process safety, reliability, asset integrity, and technical business acumen. To elevate your engineering solutions, please contact us today.